Lexikon der Chemie: Cracken
Cracken (engl. to crack "spalten"), ein Verfahren zur Umwandlung von Kohlenwasserstofffraktionen in solche mit niedriger Durchschnittsmolekülmasse. Die Crackverfahren gestatten es, die Ausbeuten an den verschiedenen Erdölfraktionen der Rohöldestillation dem Bedarf anzupassen. Bei Temperaturen zwischen 450 und 650 °C werden die großen Kohlenwasserstoffmoleküle dieser Erdölbestandteile in endothermer Reaktion gespalten. Dabei entstehen niedrigsiedende Kohlenwasserstoffe (Benzin) und Spaltgase, wie Wasserstoff, Methan, Ethan, Propan, Butan, Ethen, Propen, Buten. Diese sind Ausgangsmaterial für weitere chem. Verfahren (Petrochemie). Zu den Crackprozessen im weiteren Sinne rechnet man auch die Pyrolyseprozesse, die bei Temperaturen oberhalb 600 °C bis über 2000 °C stattfinden und eine tiefgreifende Spaltung des Einsatzproduktes bewirken, so daß in erster Linie gasförmige Reaktionsprodukte entstehen (Pyrolyse).
Das C. erfolgt entweder rein thermisch oder katalytisch. Da die hierbei unter anderem entstehenden verzweigten Alkane höhere Klopffestigkeit als die unverzweigten Alkane besitzen, sind katalytisch gewonnene Crackbenzine qualitativ besser als thermische.
1) Thermisches C. (Tieftemperaturcracken). Je nach Arbeitsbedingungen unterscheidet man zwischen Flüssigphasecracken (Visbreaken) bei Drücken von 1 bis 7 MPa und Temperaturen von etwa 500 °C und Gas- oder Gemischtphasecracken, bei dem unter Temperaturen bis zu 600 °C das Einsatzprodukt in weitgehend verdampftem Zustande vorliegt; der Druck wird hierbei wesentlich niedriger gehalten. Das thermische C. verläuft nach einem Radikalkettenmechanismus (Pyrolyse).
Die ältesten Flüssigphasecrackprozesse wurden diskontinuierlich in großen Blasen durchgeführt, die man auf 500 bis 600 °C erhitzte. Eine grundlegende Verbesserung der Technologie war durch die Einführung des Röhrenofens möglich. Hierbei wird das Öl kontinuierlich in mit Ölfeuerung beheizten Edelstahlrohren auf Cracktemperatur unter Druck aufgeheizt. Durch geeignete technologische Maßnahmen wird die Koksbildung in Grenzen gehalten. Im Gegensatz hierzu beläßt man bei der "Verkokungsfahrweise" das im Röhrenofen aufgeheizte Einsatzprodukt in besonderen Kokskammern lange auf Cracktemperatur, bis die Koksbildung abgeschlossen ist. Der sich in den Kammern abscheidende Petrolkoks wird mechanisch entfernt und stellt infolge seines niedrigen Aschegehaltes ein wertvolles Ausgangsprodukt z. B. für Elektrodenkohlen dar. Nach diesem Prinzip arbeitet z. B. das Delayed-Coking-Verfahren.
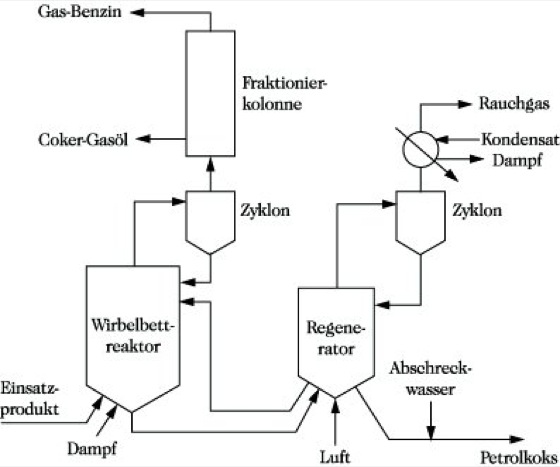
Cracken. Abb. 1: Fluid-Coking-Verfahren.
Eine Weiterentwicklung stellt das Fluid-Coking-Verfahren (Abb. 1) dar. Hierbei werden die heißen Dämpfe schwerer Rückstandsprodukte bei 500 bis 570 °C in einen Wirbelbettreaktor, dessen Wirbelbett aus heißen Kokskörnern besteht, eingeblasen. Der Koks wird ständig im Kreislauf durch einen Regenerator geführt, in dem unter Zusatz von Luft ein geringer Teil des Kokses verbrannt wird. Die hierbei freiwerdende Wärmemenge dient der Unterhaltung der endothermen Crackreaktion. Der Überschuß an Koks wird kontinuierlich au der Anlage ausgetragen. Die Feinstaubabscheidung erfolgt mit Hilfe von Zyklonen. In einer Fraktionierkolonne wird das Crackprodukt in Gas-Benzin und Coker-Gasöl getrennt.
Moderne thermische Anlagen, z. B. für das Dubbs-Verfahren, arbeiten meist mehrstufig. Dabei werden die schwersten Anteile des Einsatzproduktes auf Koks und die leichten und mittleren Fraktionen unter Anpassung der Reaktionsbedingungen an das jeweilige Zwischenprodukt selektiv auf Heizöl und Benzin gespalten (Selektivcracken).
An Bedeutung zugenommen haben die thermischen Verfahren der Rückstandscrackung, die in erster Linie die Aufarbeitung schwerer Rückstände in Produkte geringerer Viskosität bezwecken (Visbreaken). Derartige Produkte dienen entweder unmittelbar als Heizöle oder aber als Einsatzprodukte für katalytische Crackverfahren. Man arbeitet hierbei unter relativ milden Bedingungen, bei denen lediglich die hochmolekularen Inhaltsstoffe gering gespalten werden.
2) Katalytisches C. (Katcracken, Catcracking). Dieses Crackverfahren liefert wie das thermische C. Gas, Benzin und höhersiedende Anteile. Die katalytischen Crackprozesse werden, von wenigen Ausnahmen (z. B. Houdresid-Verfahren) abgesehen, in der Dampfphase durchgeführt. Die Temperaturen liegen zwischen 460 und 500 °C, die Drücke zwischen 0,1 und 0,15 MPa. Die Katalysatoren bestehen zu etwa 10 % aus Aluminiumoxid Al2O3 und zu 90 % aus Siliciumdioxid SiO2; auch Magnesiumsilicate können eingesetzt werden. Große Bedeutung haben durch Ionenaustausch modifizierte Zeolithe (X- und vor allem Y-Molekularsiebe) als Katalysatoren für Crackverfahren. Die Reaktion verläuft über Carbenium-Ionen, dabei können neben der eigentlichen Crackreaktion auch Isomerisierungs- und Polymerisierungsreaktionen eintreten. Daneben bilden sich durch Dehydrierung von Naphthenen Aromaten.
Während des Crackprozesses schlägt sich Koks auf dem Katalysator nieder und vermindert die Aktivität. Durch Abbrennen des Kokses mit Luft bei Temperaturen von 600 bis 680 °C wird der Kontakt von Zeit zu Zeit regeneriert. Der Anfall an Koks und Gas ist beim katalytischen C. geringer als beim thermischen C.; deshalb können die Umsätze bei einmaligem Durchsatz durch den Crackofen wesentlich höher als beim thermischen Verfahren gewählt werden.
Man unterscheidet drei Arbeitsweisen: Festbettverfahren, Bewegtbettverfahren und Wirbelbettverfahren.
a) Die Festbettverfahren (Fixed-Bed-Verfahren), erstmalig 1936 von Houdry eingeführt, haben heute keine Bedeutung.
b) Von den Bewegtbettverfahren (Wanderbettverfahren, Moving-Bed-Verfahren), 1940 ebenfalls von Houdry entwickelt, sind das TCC-Verfahren und das Houdry-flow-Verfahren von Bedeutung. Beim TCC-Verfahren (Thermofor-Catalytic-Cracking-Verfahren) rieselt der meist pulverförmige Katalysator unter dem Einfluß der Schwerkraft durch den Reaktor (Reaktionstemperatur 450 bis 510 °C). Der verkokte Katalysator gelangt in den tiefer gelegenen Regenerator und wird dort mit Hilfe von Luft regeneriert (die Kohlenstoffablagerungen werden dabei abgebrannt). Der regenerierte Katalysator wird durch pneumatischen Transport in den Reaktor zurückgeführt. Die Crackdämpfe werden in einer Fraktionierkolonne aufgearbeitet. Das Houdryflow-Verfahren unterscheidet sich nicht grundsätzlich vom TCC-Verfahren. Wesentlicher Unterschied ist, daß der pneumatische Transport des regenerierten Katalysators nicht mit Luft, sondern mit Rauchgas erfolgt.
c) Von den Wirbelbettverfahren (Fluid-Bed-Verfahren) ist am wichtigsten das FCC-Verfahren (Fluid-Catalytic-Cracking-Verfahren, Abb. 2). Die erste Anlage nach dem FCC-Verfahren ging 1942 in Betrieb (Standard Oil Co. of New Jersey). Man arbeitet mit einem Katalysator, der in feinster Staubform mit einer Korngröße von 0,05 bis 0,2 mm vorliegt und sich mechanisch, ähnlich einer Flüssigkeit, verhält. Er ermöglicht leichteren Transport, gleichmäßigere Wärmeverteilung und gute Wärmeübertragung an das Spaltgut. Der Katalysator wird auf 500 bis 550 °C erhitzt und bringt das Spaltgut zum Verdampfen. Die Öldämpfe wirbeln den staubfeinen Katalysator durch die Reaktionszone, so daß das C. durch die innige Vermischung nach kurzer Zeit vollzogen ist. Im Reaktor herrscht ein Druck von 0,07 MPa.
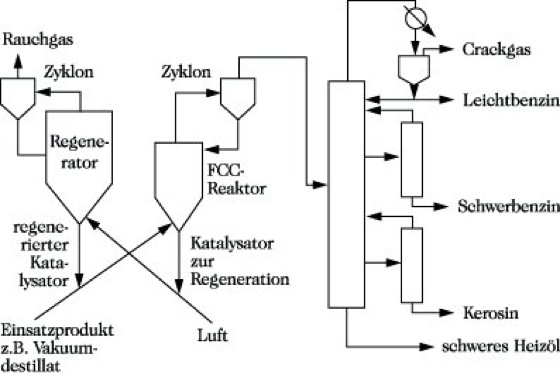
Cracken. Abb. 2: Schema einer FC-Anlage.
Das aus dem Reaktor austretende Öldampf-Katalysator-Gemisch wird in einem Zyklon getrennt, und der koksbeladene Katalysator wird durch einen Luftstrom in den Regenerator getragen, in dem der Koks abgebrannt wird. Die in den Abgasen enthaltene Wärme zieht man zur Dampferzeugung heran. Die Öldämpfe gelangen in eine Fraktionierkolonne, die sie in Benzin, Gasöl und Heizöl, Kreislauföl und Rückstand zerlegt. Als Katalysatoren für das FCC-Verfahren werden Alumosilicate oder modifizierte Zeolithe eingesetzt. Zur Entfernung von ungesättigten Verbindungen, insbesondere Diolefinen, müssen die erhaltenen Fraktionen noch einer Hydroraffination unterzogen werden. Als Crackreaktoren werden auch Flugstaub- oder Riser-Reaktoren eingesetzt. Dabei durchströmt der eingesetzte Kohlenwasserstoff zusammen mit dem heißen Katalysator ein Steigrohr (Riser), in welchem nach etwa 5 Sekunden Verweildauer die Crackreaktionen beendet sind.
3) Katalytisches C. in Gegenwart von Wasserstoff. Wasserstoffarme Fraktionen (Rückstandsöle) sind für das katalytische C. nicht geeignet. Der niedrige Wasserstoffgehalt und die in den Rückstandsölen vorhandenen Heteroverbindungen bewirken eine schnelle Desaktivierung des Katalysators. Rückstandsöle werden darum vorteilhaft in Gegenwart von Wasserstoff gecrackt (Hydrocracken, Hydrospalten).
4) Pyrolyseprozesse. Sie haben sich aus den Dampfphase-Crackprozessen entwickelt und ermöglichen es, aus nieder- oder höhermolekularen Ausgangsmaterialien vorwiegend gasförmige Alkene und in gewissen Mengen aromatische Kohlenwasserstoffe herzustellen, die bei den vorher beschriebenen Crackprozessen nur als Nebenprodukte anfallen. Alle Verfahren dieser Art werden drucklos bei hohen Temperaturen oberhalb 600 °C betrieben.
Bei den Pyrolyseprozessen treten zwei Grundreaktionen auf: Crackprozesse, bei denen ein langkettiges Alkan in ein kürzerkettiges Alkan und ein Alken zerfällt, und Dehydrierprozesse, bei denen ein Alkan unter Wasserstoffabspaltung in ein Alken übergeführt wird. Je länger die Kohlenstoffkette ist, desto mehr überwiegt die Crackreaktion gegenüber der Dehydrierreaktion (Pyrolyse).
Wenn Sie inhaltliche Anmerkungen zu diesem Artikel haben, können Sie die Redaktion per E-Mail informieren. Wir lesen Ihre Zuschrift, bitten jedoch um Verständnis, dass wir nicht jede beantworten können.