Lithium-Ionen-Akkus: Die Altlast der Elektromobilität
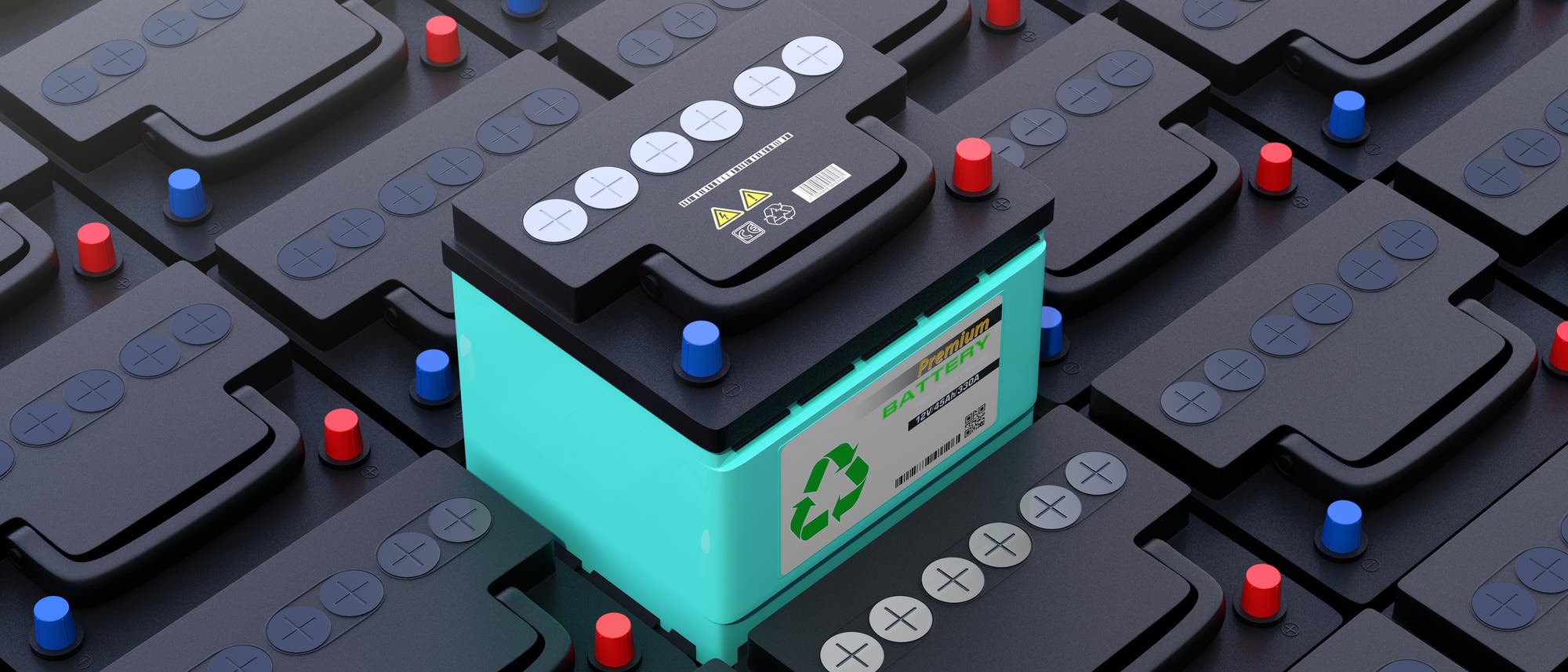
Wenn frisch gekürte Nobelpreisträger die Nachricht aus Stockholm erhalten, erzählen sie in Interviews oft von den Anfängen ihrer Entdeckung. Der Japaner Akira Yoshino, 2019 mit dem Nobelpreis für Chemie geehrt, sprach hingegen über das Ende der von ihm mitentwickelten Lithium-Ionen-Akkus: »Es kommt darauf an, ob diese Batterien recycelt werden können«, sagte er.
Seit den frühen 1990er Jahren versorgen die leistungsfähigen Energiespeicher Videokameras und Handys, damals maß man ihr Gewicht in Gramm. Inzwischen sind sie zentnerschwer und enthalten die Antriebsenergie von Elektroautos. Damit sind sie ein wesentlicher Teil der Hoffnung, den Straßenverkehr klimafreundlicher zu gestalten.
Kosten, Leistung, Ausdauer
Dazu müsste man viele Bestandteile der Akkus allerdings wiederverwerten, finden Nobelpreisträger Yoshino und andere Experten. Doch dieser Gedanke hat die Heerscharen von Batterieentwicklern bisher kaum erreicht. Die geplante und effiziente Wiederverwertung der Energiespeicher ist bei vielen von ihnen noch immer ein nachrangiges Designkriterium, wenn überhaupt. Stattdessen geht es vor allem um Kosten, Leistung, Ausdauer und die Integration in möglichst attraktive Elektroautos.
Jens Peters beobachtet diesen Missstand schon lange. »Die Batteriepacks sind meist verschweißt oder verklebt und normalerweise nicht dafür gebaut, jemals wieder aufgemacht zu werden«, sagt der Elektroingenieur. Er hat lange am Karlsruher Institut für Technologie (KIT) zu Energiespeichern geforscht, seit Kurzem ist er Professor an der Universidad de Alcalá im Großraum Madrid.
Heute kämen nur wenige der Batterien ins Recycling, sagt Peters. Und wenn sie dort landen, dann auf Initiative der Hersteller. Keine zukunftsfähige Lösung, findet der Fachmann. »Wenn Elektroautos irgendwann 50 Prozent der Fahrzeuge ausmachen und eine unübersehbare Vielfalt von Batterien 15 oder 20 Jahre nach Fertigung entsorgt werden muss, stehen die Firmen allein da.« Was man stattdessen bräuchte: eine funktionierende Recycling-Wirtschaft, die möglichst viele Bestandteile der Akkus aus E-Autos wiederverwendet.
Aber der Weg dorthin ist voller Hindernisse. Heutige Batteriepacks lassen sich kaum demontieren, gezielt oder automatisiert geht es schon gar nicht. Das freundliche Wort »Recycling« bedeutet meist: aufreißen, schreddern, rösten, mit Schockwellen oder Laugen und Säuren behandeln, einschmelzen, teilweise abfackeln, zu Füllmaterial für Zement reduzieren. Nachhaltig sieht anders aus.
Recycling als Kostenfaktor
Und ob sich die heutigen Verfahren am Ende auszahlen, finanziell oder für die Umwelt, ist fraglich. Eine entsprechende Verwertung von Lithium-Ionen-Akkus, sowohl aus Elektrogeräten wie aus Fahrzeugen, kostet zurzeit bis zu 3000 Euro pro Tonne, schätzt das Umweltbundesamt. Gilt das in Zukunft auch für die Energiespeicher von Elektroautos, bedeutet das 700 bis 1600 Euro pro Autowrack. Wohlgemerkt: Eine wiederverwendbare Batterie hat man damit nicht. Man kann lediglich darauf hoffen, manche der Bestandteile in anderen Produkten wiederzuverwenden.
Entsprechend warnen Experten seit Langem vor einem Berg funktionsunfähiger Batterien, die sich im Schatten des E-Auto-Booms anhäufen könnten. Schätzungen zufolge werden bis 2030 elf Millionen Tonnen alter Akkus anfallen, Jahr für Jahr sollen danach weitere zwei Millionen Tonnen dazukommen. Für Deutschland rechnet das Umweltbundesamt mit einer Menge von 30 000 Tonnen pro Jahr. Immerhin: Die sechs »Recycling«-Anlagen, die es hier zu Lande bereits gibt, könnten bereits 21 000 Tonnen verwerten.
Trotzdem stehen der Branche schwierige Richtungsentscheidungen bevor, warnt Jens Peters: »Ein Grundproblem ist, dass man Prozesse und Anlagen planen muss und dabei nicht weiß, wie die Batterien der Zukunft aussehen werden.« Offen sei auch, welche zurückgewonnenen Materialien künftig gefragt sein werden und welche Form sie dazu haben müssten.
Ein Nachleben für alte Akkus
Fragen wie diesen widmen sich derzeit überall auf der Welt Projekte und Forschungsverbünde, in denen Hochschulen und Firmen zusammenarbeiten. Einige der Initiativen verfolgen dabei schlicht das Ziel, Autobatterien länger zu nutzen. Sie versuchen beispielsweise, die Energiepakete gezielt zu reparieren oder nur die verbrauchten Komponenten auszusortieren und auszutauschen, die die Leistung eines ganzen Batteriepacks nach unten ziehen.
Vergleichsweise etabliert ist auch die Strategie von Autoherstellern und anderen Firmen, die Aggregate nach den Jahren auf der Straße noch eine Weile in Kellern oder Hallen zu nutzen, wo sie unter ruhigeren Bedingungen erneuerbaren Strom zwischenspeichern. Wie groß allerdings der Anteil der Batterien sein wird, die für ein Nachleben in der einen oder anderen Form fit genug sind, ist fraglich. Und auf Dauer werden diese Initiativen die Mengen nutzloser Autobatterien nicht reduzieren, sondern ihre Ankunft auf dem Recyclingmarkt nur verzögern.
Dort müssen sich Planer und Mitarbeiter mit dem komplizierten Innenleben der Batterien auseinandersetzen. Ein Batteriepack besteht aus einem oder etlichen Dutzend Modulen, in denen wiederum mehrere bis hunderte Zellen zusammengeschaltet sind. Hinzu kommen Anschlüsse und Ladeelektronik, Gehäuse und mechanische Verstärkungen. Das alles wird an die Platzverhältnisse im Auto angepasst und für mögliche Unfälle versteift und verkapselt. Bei Wagen mit großer Reichweite und hohem Preis erreichen Batteriepacks eine halbe Tonne an Masse und viele hundert Liter Volumen.
Schaut man genauer hin, wird die Sache noch komplexer: Auf der Zellebene, dem eigentlich aktiven Part des Aggregats, sind viele Schichten zusammengepresst oder -gewickelt und mit einer eigenen, hermetischen Hülle versehen. So kann das Bauteil die Form eines Zylinders, eines Quaders oder einer flachen, leicht biegsamen Tasche annehmen.
Im Inneren finden sich die beiden Elektroden: Die Kathode besteht meist aus einem keramischen Pulver von Lithiumoxid-Metallverbindungen auf einer Aluminiumfolie. Die enthaltenen Metalle wie Nickel und vor allem Kobalt sind teuer und wertvoll; sie wiederzugewinnen, treibt heute oft die Recyclingbemühungen. Die Anteile von Mangan, Eisen, Phosphor oder Aluminium sind den Verwertern weniger wichtig.
Die Anode, der Pluspol, besteht dagegen üblicherweise aus einer Graphitschicht auf Kupfer. Eine Art Polymer-Klebstoff hält die pulvrigen Materialien auf beiden Seiten an den jeweiligen Metallfolien fest. Zwischen den Elektroden befindet sich ein dünner, durchlöcherter Plastikfilm zur Isolierung, der auf beiden Seiten von Elektrolyt umgeben ist, einer meist lithium- und fluorhaltigen, Strom leitenden Flüssigkeit. Hier bewegen sich die Lithium-Ionen, die dem Batterietyp seinen Namen gegeben haben, zwischen den Elektroden. Beim Laden oder Entladen schlüpfen sie in die porösen Materialien auf beiden Seiten.
Problematische Restenergie
Wer ein solches Batteriepack recyceln will, muss zunächst ein naheliegendes Hindernis überwinden: Oft enthalten alte Akkus noch Energie, mitunter stehen sie auch unter Druck. Doch gesicherte Informationen über Bauweise und absolvierte Ladezyklen sind oft schwierig zu bekommen. Einige Unternehmen machen aus dieser Not bereits eine Tugend: Sie nutzen den gespeicherten Reststrom, um Wärme zu erzeugen, oder speisen ihn ins Netz.
Anschließend beginnen Mitarbeiter mit der händischen Demontage. Gehäuse, Kabel und Elektronik liefern dabei relativ sortenrein Aluminium, Stahl und Kupfer. Aber schon bei diesem Schritt erschweren Schweißverbindungen und Verklebungen an den Batteriemodulen die Demontage, wie die Teilnehmer eines Workshops am Karlsruher Institut für Technologie, den Jens Peters mitorganisiert hatte, 2018 festhielten.
Das Problem ist Experten schon länger bekannt. Man solle doch mehr »Schrauben und Muttern« verwenden, um die Trennung der Komponenten zu vereinfachen, forderte die US-amerikanische Wissenschaftlerin Linda Gaines vom Argonne National Laboratory bereits 2015 im Fachmagazin »Nature«. Allerdings haben sich bisher weder diese noch andere Lösungen durchgesetzt. Manche Forscher erproben immerhin, ob Wärme oder Schockwellen in einem Wasserbad dabei helfen können, die Verklebungen zu lösen.
Trotzdem bleibt die äußere Demontage der einfache Teil. Sobald es daran geht, Module oder gar Zellen zu öffnen, müssen weitere Vorsichtsnahmen greifen. Die fluorhaltigen Elektrolyte dürfen nicht austreten, sie sind toxisch und leicht brennbar – unter anderen deshalb sind die Batteriepacks hermetisch gesichert, damit Elektroautos nicht nach Auffahrunfällen in Flammen aufgehen. Die Entsorgung der Flüssigkeit oder der Dämpfe beim Abfackeln erfordert höchste Standards in der Abgaskontrolle. Das stelle »eine der größten Herausforderungen für die Prozesskette dar«, waren sich die Experten in Karlsruhe einig.
Einschmelzen bei 1500 Grad
Darum werden die Module oft unter Luftabschluss zerstört, hauptsächlich mit zwei verschiedenen Verfahren. Da ist zunächst die so genannte Pyrometallurgie, bei der man die Batterien bei bis zu 1500 Grad einschmilzt. Mit ihr arbeitet zum Beispiel die Firma Umicore an ihrem Standort in Hoboken/Belgien und die Nickelhütte in Aue im Erzgebirge. Bei dem Verfahren bleibt am Ende eine Legierung der wertvollen Kathoden-Metalle Kobalt, Nickel und Kupfer übrig, die noch weiter getrennt werden müssen, um sie sortenrein verkaufen zu können. Der Aufwand, der in die Herstellung des keramischen Kathoden-Pulvers geflossen ist, geht so verloren.
Kunststoffe, Elektrolyte, Graphit und andere Stoffe verbrennen im Schmelzofen womöglich einfach und verbessern so die energetische Bilanz des Prozesses, oder sie landen teilweise in einer amorphen schwarzen Masse. Das Lithium kann dann zusammen mit Anteilen von Seltenen Erden als Konzentrat an einen Verwerter geliefert werden – so hält es Umicore.
»Die Folgen für die Umwelt wären in einer gut gemanagten Müllkippe viel geringer«
Rebecca Ciez, Columbia University
Diese weitere Aufspaltung der Reste und zum Beispiel das Zurückgewinnen des Lithiums sind zwar möglich, wie Forschungsprojekte ergaben. Sie lohnen sich aber finanziell häufig nicht oder erfordern einen unverhältnismäßigen Einsatz von Energie, wie der KIT-Workshop zeigte. Amerikanische und britische Experten kamen 2019 in »Nature« zu einem ähnlichen Schluss.
Oft genug bilden Lithium, Mangan sowie Aluminium nach dem pyrometallurgischen Recycling dagegen eine Art Asche, die Zementhersteller verwenden können. Wenn das geschieht, selbst wenn die Schlacke aus dem Einschmelzen wie bei anderen Batterietypen im Straßenbau verwendet wird, gilt es aktuell als erfolgreiches, »stoffliches« Recycling: Laut europäischen Bestimmungen muss dafür nur die Hälfte der Batteriemasse wiederverwendet werden. Dazu zählt auch das so genannte Downcycling, wenn Reste eines Hightech-Produkts in Fahrbahnen oder Rohbauten landen.
Die Alternative: Akkus zerschreddern
Die andere wichtige Methode der Verwertung nennt sich Hydrometallurgie. Dafür werden die Batteriezellen unter Luftabschluss geschreddert. Dann lassen sich einige der Trümmer magnetisch oder mechanisch sortieren, mit Sieben oder anhand der Dichte. Außerdem kommen ätzende Flüssigkeiten wie Schwefelsäure oder Wasserstoffperoxid zum Einsatz, um Metalle aus den Fetzen der Batterie auszulaugen oder auszufällen. Die Temperaturen liegen dabei eher bei 100 Grad Celsius.
Die deutsche Firma Duesenfeld mit Sitz in der Nähe von Braunschweig sammelt bei einem solchen Prozess nach eigener Darstellung auch die Elektrolytflüssigkeit, das Lithium und das Graphit. Volkswagen baut zurzeit eine Recyclinganlage nach diesem Prinzip auf.
Eine weitere Variante des Recyclings nutzt das Unternehmen Accurec in Krefeld: Dort erhitzen Mitarbeiter die Batteriemodule zunächst auf einige hundert Grad, damit sich Elektrolyte und Kunststoffe unter Sauerstoffabschluss zersetzen und Verklebungen sich lösen. Danach erst beginnt der weitere Prozess mit dem Zerkleinern der abgekühlten, oft schon verformten Reste. Zurzeit läuft dort ein vom Bundesumweltministerium gefördertes Projekt, das die Kobalt-Nickel-Fraktion der Kathode als »produktfähiges Pulver« gewinnen und auch das Graphit und Lithium industriell weiterverarbeiten will.
Keines der Verfahren ist der nötige Durchbruch
Beide Grundverfahren des Batterierecyclings, das Schmelzen und das Auslaugen, überzeugen Experten jedoch nicht recht. Die Autoren des »Nature«-Artikels aus dem Jahr 2019 schreiben zum Beispiel: »Es ist klar, dass das momentane Design von Batteriezellen das Recycling extrem kompliziert macht und dass weder Hydro- noch Pyrometallurgie zu reinen Strömen von Material führen, die sich einfach in ein Kreislaufsystem für Batterien einspeisen lassen.«
Besser würde wohl eine Methode abschneiden, die direktes Recycling heißt. Es soll das keramische Lithium-Metall-Pulver auf der Kathodenseite, in dessen Herstellung ja schon viel Mühe und Energie geflossen ist, möglichst in seiner ursprünglichen oder einer für neue Aggregate tauglichen Form wiederherstellen. Dabei ergibt sich aber das Problem, dass das Material womöglich aus verschiedenen Batterietypen stammt, deren Zusammensetzung gar nicht genau bekannt ist und Jahrzehnte nach der Herstellung sowieso nicht mehr den aktuellen Anforderungen der Produzenten entspricht.
»Wenn die Autohersteller damit beginnen würden, auf das spätere Recycling zu achten, wären viele der Probleme leichter zu lösen«
Jens Peters, Universidad de Alcalá
Darum sieht das Verfahren vor, die Module zu zerkleinern und das isolierte Pulver mit Metallverbindungen in der nötigen Menge zu ergänzen. So ließe sich zum Beispiel das erwünschte Verhältnis von Mangan, Nickel und Kobalt herstellen, die in einem derzeit viel verwendeten Batterietyp Dienst tun. Und dann liegt das Material für lange Zeit in einer Reaktionsflüssigkeit, bis sich Partikel der erwünschten Korngröße gebildet haben.
Eine Woche hat das bei einem Versuch gedauert, den Forscher des Worcester Politechnic Institute in Massachusetts mit Entwicklern verschiedener Firmen unternommen haben. Das Team hatte 30 Kilogramm Batteriemodule aus Autos von Chevrolet, Ford und Fiat zusammen verarbeitet. Das ist ein Fortschritt, denn in einem ersten Versuch war die recycelte Menge bloß ein Kilogramm schwer. Dennoch dürfte der Weg zum industriellen Maßstab noch weit sein.
Nur mit einer solchen Methode aber lohnt sich das Recyceln der Batteriezellen womöglich auch für das Klima, zeigen erste Daten. In Deutschland hatte das Öko-Institut im Jahr 2016 Ökobilanzen für wissenschaftliche Recyclingprojekte aufgestellt, die den Verfahren bei den Firmen Accurec und Duesenfeld zu Grunde liegen. Die Prüfer erteilten durchweg gute Noten. Doch uneingeschränkt positiv war die Bilanz nur für die anfängliche Demontage der Batteriepacks. Für die »Aufbereitung des Aktivmaterials« in den Zellen ergaben sich für Treibhauspotenzial und Primärenergiebedarf keine »Nettogutschriften«, wie es die Kontrolleure formulierten. Fürs Klima war das Verwerten der Zellen also eher eine Belastung.
Überschaubarer Nutzen für die Umwelt
Ähnlich sehen Wissenschaftler der Carnegie Mellon University die Verfahren, wie sie 2019 in »Nature Sustainability« berichteten: Nur direktes Recycling, das freilich noch in den Kinderschuhen steckt, kann demnach verlässlich helfen, CO2-Emissionen zu verhindern. Aus zylindrischen Zellen, auf die beispielsweise Tesla setzt, muss man damit aber etwa 90 Prozent des Kathodenmaterials wiedergewinnen, aus Zellen im Taschenformat ungefähr 60 Prozent. »Pyro- und hydrometallurgische Prozesse haben keine Umweltvorteile«, urteilte das Autorenteam um Rebecca Ciez. Eine Einschätzung, die die Ingenieurin, die mittlerweile an der Columbia University in New York arbeitet, gegenüber »Spektrum.de« nochmals unterstreicht: »Die Folgen für die Umwelt wären in einer gut gemanagten Müllkippe viel geringer«, schreibt Ciez per E-Mail.
Allerdings zeigen sich beim Recycling auch Zielkonflikte und Unsicherheiten. Diese können die Wirtschaftlichkeit betreffen: Zurzeit mag es sich lohnen, Kobalt aus den Zellen zurückzugewinnen. Doch da die Preise schwanken und Produzenten seit Langem versuchen, immer weniger von dem teuren Metall zu verwenden, kann sich das Blatt auch wenden. Beim Lithium ist es umgekehrt: Dort rechnet sich die aufwändige Wiederaufbereitung aktuell nicht, urteilten die Experten auf dem KIT-Workshop. Denn der Neuabbau des Leichtmetalls ist preiswerter und teils sogar ökologischer als das Recycling. Was wohl einiges über den bisherigen Stand der Wiederaufbereitungstechnik aussagt: Lithium wird derzeit oft unter umstrittenen Bedingungen im bolivianischen oder chilenischen Hochland gefördert und um den halben Planeten transportiert. Ändern dürfte sich das erst, wenn die Nachfrage durch einen Elektroauto-Boom steigt und andere Quellen des Elements erschlossen werden.
In der Herkunft der Batteriemetalle kann man auch ein moralisches Argument für eine weitere Verbesserung des Recyclings sehen: 60 Prozent des Kobalts auf dem Weltmarkt kommt heute aus der Demokratischen Republik Kongo, wo Armut und politische Instabilität zu Zwangs- und Kinderarbeit unter haarsträubenden Bedingungen führen. Das lässt es eigentlich geboten erscheinen, jedes Gramm Metall wiederzugewinnen, zumal die gesellschaftliche Verantwortung von Firmen zunehmend an der Herkunft ihrer Rohstoffe gemessen wird.
Und dann gibt es industriepolitische Fragen: Was soll man in Deutschland mit dem recycelten Material, wenn die Batterien ohnehin zurzeit in Asien hergestellt werden? Baut man hier eine eigene Produktion auf, so dass man die Rohstoffquelle Altbatterie unbedingt sichern will? Was passiert, wenn das Zerlegen in Billiglohnländern einfach preiswerter ist: Wer achtet dann auf die Abgasreinigung und die Umweltschäden durch Fluor-Elektrolyte? Und wie weit treibt man sinnvollerweise die Wiederverwertung der teuren Batteriepacks?
Jens Peters und seine Kollegen verdichten solche Zielkonflikte im Begriff »Recycling-Tiefe«. Sie ist eine von vielen offenen Fragen, für die Ingenieure in den kommenden Jahrzehnten eine Antwort finden müssen. Eines ist Peters und seinen Kollegen schon jetzt klar: »Wenn die Autohersteller damit beginnen würden, auf das spätere Recycling zu achten und es vorzubereiten, wären viele der Probleme leichter zu lösen.«
Wenn Sie inhaltliche Anmerkungen zu diesem Artikel haben, können Sie die Redaktion per E-Mail informieren. Wir lesen Ihre Zuschrift, bitten jedoch um Verständnis, dass wir nicht jede beantworten können.