Methanisierung: Boost für Biomasse
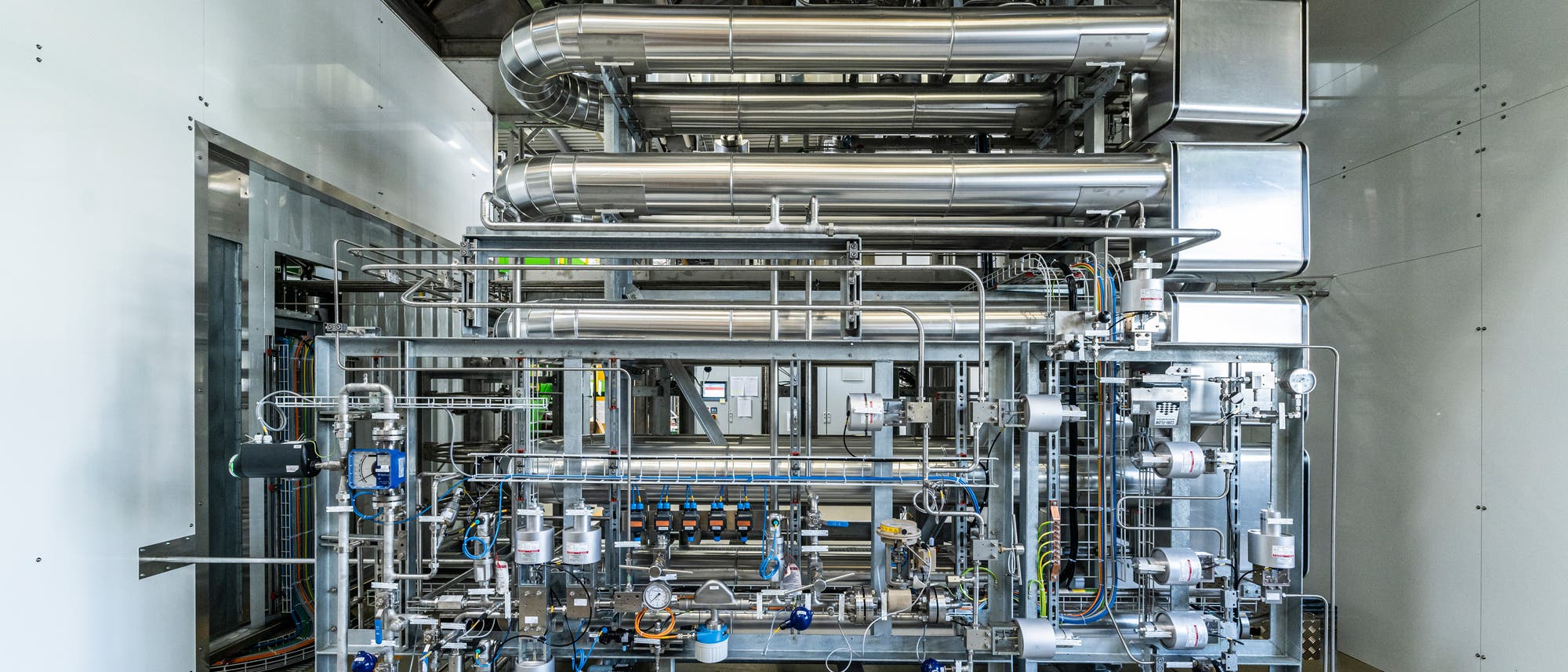
Aus Biomasse und organischem Abfall wurden im Jahr 2022 deutschlandweit etwa 50,2 Milliarden Kilowattstunden (kWh) Strom erzeugt. Damit ist Biomasse zurzeit der wichtigste erneuerbare Energieträger hier zu Lande: Sie liefert insgesamt 52 Prozent der erneuerbaren Energie – nicht nur als Biogas zur Stromerzeugung, sondern auch in anderer Form, etwa als Holz zum Heizen. Windenergie trägt 26 Prozent bei, Sonnenenergie 14 Prozent, Wasserkraft und Geothermie je 4 Prozent, wie das Bundesministerium für Ernährung und Landwirtschaft BMEL bekannt gibt.
Ganz unumstritten ist die Nutzung von Biomasse nicht. Etwa weil Energiepflanzen an Stelle von Nahrungspflanzen auf den Äckern stehen oder Holz wegen der steigenden Nachfrage direkt zum Verbrennen geerntet wird, statt es als Bauholz zu nutzen und lediglich das verbleibende Restholz zu Hackschnitzeln oder Pellets zu verarbeiten.
Dennoch will das BMEL künftig noch stärker auf Biomasse setzen, um Energie für Wärme, Verkehr und Strom zu erzeugen. Dazu sollen zunehmend Reststoffe und Abfälle biologischen Ursprungs in den Fokus rücken: etwa Alt- und Gebrauchtholz, Bioabfall, Gülle und Mist. Also Stoffe, die ohnehin vorhanden sind und nicht mit der Nahrungsmittelproduktion konkurrieren.
Der Weg dahin ist aber noch weit. Bislang werden nicht einmal die in der Landwirtschaft anfallenden Reststoffe Mist und Gülle in nennenswertem Maß zu Biogas verarbeitet, aus dem sich dann Strom gewinnen lässt. Denn solche Anlagen lohnen sich häufig nur dann, wenn sich mehrere Betriebe zusammentun.
Biomethan-Anlage mit außergewöhnlichem Wirkungsgrad
In der Schweiz wollen jetzt vier Forschungsinstitute der energetischen Nutzung von Biomasse einen entscheidenden Schub verleihen – und zwar, indem sie Klärschlamm effizient zu Biogas verarbeiten. Der Stoff fällt ständig in großen Mengen an, gilt jedoch als besonders schwierig zu nutzen, weil seine chemische Zusammensetzung stark schwankt. Ausgerechnet mit diesem Material ist es nun gelungen, den Wirkungsgrad sprunghaft zu erhöhen – das erzeugte Biomethan enthält 60 bis 70 Prozent der im Ausgangsmaterial enthaltenen Energie.
Das war bis vor Kurzem noch kaum vorstellbar. Große herkömmliche Biogasanlagen schaffen gerade einmal um die 40 Prozent, nachdem man den Eigenbedarf für den Betrieb abzieht. Kleinere Anlagen, wie sie auf Bauernhöfen zum Einsatz kommen, erreichen gar nur 30 Prozent. Denn das Zusammenspiel der Mikroorganismen, die beispielsweise in herkömmlichen landwirtschaftlichen Biogasanlagen für die nötige Vergärung sorgen, lässt sich schwer steuern oder optimieren. Die Mikroben verwerten bloß, was ihnen behagt, und lassen alles andere liegen, was sich gewaltig auf die Energiebilanz auswirkt. Für die Hochtemperaturvergasung wiederum, wie sie etwa bei Holz eingesetzt wird, müssten die feuchten Ausgangsstoffe erst getrocknet werden – ein energieintensiver Prozess, durch den die Nettoenergieausbeute sehr gering ausfallen würde.
Um die problematischen Biomassen trotzdem für technische Prozesse nutzbar zu machen, haben Fachleute am Paul Scherrer Institut (PSI) in der Schweiz 20 Jahre Arbeit in eine bisher wenig beachtete Methode investiert, die hydrothermale Vergasung. Mittlerweile verarbeiten sie in ihrer Pilotanlage 100 Kilogramm Klärschlamm pro Stunde. Ein entscheidender Vorteil: Der Klärschlamm muss nicht mehr ganz getrocknet werden, sondern lediglich so weit entwässert, dass er zumindest 10 bis 20 Prozent Trockensubstanz enthält. Nach Optimierungen und Erfahrungen an der Pilotanlage soll 2026 die erste große Anlage im industriellen Maßstab gebaut werden.
Enormer Druck und hohe Temperatur
Frédéric Vogel, Leiter der Gruppe Katalytische Verfahrenstechnik im Labor für Nachhaltige Energieträger und Prozesse des PSI, vergleicht die Vorgehensweise mit Vorgängen in der Erdkruste: »Im Grunde machen wir nichts anders als die Natur. Bei der Entstehung von Kohle, Erdgas oder Erdöl sind ebenfalls hydrothermale Prozesse im Spiel. Der enorme Druck und die hohen Temperaturen in der Erdkruste bewirken eine Umwandlung von abgestorbener Biomasse.« Im Gegensatz zu den geologischen Abläufen, die teils Jahrmillionen dauerten, laufe ihr Verfahren allerdings in wenigen Minuten ab. »Wir sorgen lediglich für eine millionenfache Beschleunigung dieser Prozesse«, ergänzt der Experte.
Die Schweizer betrachten das in der Biomasse enthaltene Wasser nicht als Problem bei der Energiegewinnung, das nach Möglichkeit entfernt werden muss. Im Gegenteil: Sie nutzen es als Reaktionsmedium während der hydrothermalen Vergasung. Durch hohen Druck und hohe Temperatur wird das Wasser »überkritisch« – es befindet sich also in einer Art Zwischenzustand zwischen Gas und Flüssigkeit.
In der Pilotanlage wird der flüssige Klärschlamm dazu erst unter einen Druck von 280 bis 300 Bar gesetzt und anschließend auf 360 Grad Celsius gebracht. Im nächsten Schritt wird die Flüssigkeit durch einen Salzabscheider geleitet und auf über 374 Grad Celsius weiter aufgeheizt.
Jetzt passiert das Entscheidende: Wasser geht wie gewünscht in den überkritischen Zustand über. Ob es flüssig oder gasförmig ist, lässt sich nicht mehr unterscheiden, da es so dicht ist wie eine Flüssigkeit und gleichzeitig so fließfähig wie Wasserdampf. In diesem Zustand kann man mehrere Reaktionsschritte im selben Lösungsmittel durchführen, ohne aufwändige Trennschritte. Überkritisches Wasser eignet sich daher perfekt, um organische Substanzen zu spalten, wie sie zuhauf in Biomasse vorliegen.
Die Umwandlung in überkritisches Wasser erfolgt erst im letzten Moment, weil sonst die Rohre verstopfen würden. »Ab einer Temperatur von 374 Grad fallen die in der Biomasse enthaltenen Salze aus. Der Strom in den Rohren ist an dieser Stelle abwärtsgerichtet, so dass die Salze mitgerissen werden und unten in einen Behälter ausfallen. Etwa 20 Prozent der Ursprungsmasse endet hier als Salzsole«, erläutert Vogel. Die Salze ließen sich recyceln, so dass man zum Beispiel den enthaltenen Phosphor wieder als Dünger nutzen könne.
Überkritischer Zustand
Danach wird das salzfreie Fluid auf 420 Grad aufgeheizt, die ideale Temperatur für die hydrothermale Zerlegung auf einem Katalysator, wie Testreihen gezeigt haben. Unter derartigen Bedingungen werden die großen Moleküle in der Biomasse am effizientesten in kleine zerlegt. »Diese Moleküle werden gut mit dem umgebenden Wasser durchmischt. Das sorgt dafür, dass sie anschließend besonders gut mit dem Ruthenium im Aktivkohlekatalysator reagieren«, erläutert Vogel weiter. Hierbei findet die eigentliche Reaktion statt: die Umwandlung der Moleküle aus der Biomasse in Methan (CH4), den Hauptbestandteil von Biogas, das durch Verbrennung Strom liefert.
Der Katalysator wirkt wie ein Turbobeschleuniger für die Gasbildung. Da er empfindlich gegenüber Schwefel ist, wird die Reaktionsmischung vorher noch über ein Zinkoxid-Granulat geleitet, das den enthaltenen Schwefel in Form von Zinksulfid bindet. »Entfernt man den Schwefel, bevor die Flüssigkeit in Kontakt mit dem Katalysator kommt, hält dieser deutlich länger. Der Zusatzschritt lohnt sich auf jeden Fall«, betont Vogel. Zinkoxid wiederum habe sich als extrem widerstandsfähig gegenüber den extremen Bedingungen erwiesen, die in der Anlage herrschen. »Lange nicht jedes Material hält diese hohen Temperaturen und Drücke aus«, sagt Vogel.
Das Biogas, das die Anlage verlässt, enthält etwa 55 Prozent Methan (CH4), 40 Prozent Kohlenstoffdioxid (CO2) und wenige Nebenbestandteile, darunter Wasserstoff (H2). Übrig bleibt nur Wasser mit etwas Ammoniumkarbonat, das sich als Dünger verwenden lässt.
Kein Normmaterial
Ganz allein ist das PSI mit seiner Idee nicht. Das Karlsruher Institut für Technologie (KIT) betreibt unter Leitung des Chemikers Nikolaos Boukis eine Anlage, die mit superkritischem Wasser arbeitet. Vogel kennt die dortigen Wissenschaftler gut: »Ihr Vergasungsverfahren basiert auf Temperaturen von über 600 Grad. Dafür verzichten sie auf den Katalysator. Das funktioniert ebenfalls gut. Wir haben uns unter anderem gegen diese Lösung entschieden, weil solche extremen Temperaturen die Materialauswahl stark limitieren«, erklärt er die Unterschiede.
Es hat 20 Jahre gedauert, das beste Verhältnis von Temperatur, Druck und Reaktionszeit zu finden und die Abscheidung der Salze zu handhaben. Vogel erzählt: »Eine echte Herausforderung war, den idealen Katalysator zu finden. Biomasse ist ja kein Normmaterial. Sie besteht aus hunderten Substanzen in unterschiedlichen Anteilen.«
Vogels Team betreibt die Pilotanlage aus gutem Grund mit Klärschlamm, macht sich also die Sache so schwer wie möglich. Klärschlamm sei das komplexeste Gemisch an Biomasse, das es gibt, sagt Vogel: »Wenn wir es mit Klärschlamm schaffen, dann schaffen wir es mit allem anderen erst recht.« Auch weitere Arten von Biomasse wurden getestet. So ließe sich die Anlage alternativ mit Algen betreiben und könnte selbst die Gärreste anderer Biogasanlagen verarbeiten. Sogar mit Plastik verunreinigte Biomasse ist kein Problem: Der enthaltene Kunststoff wird einfach zu Methan umgesetzt.
Schreiben Sie uns!